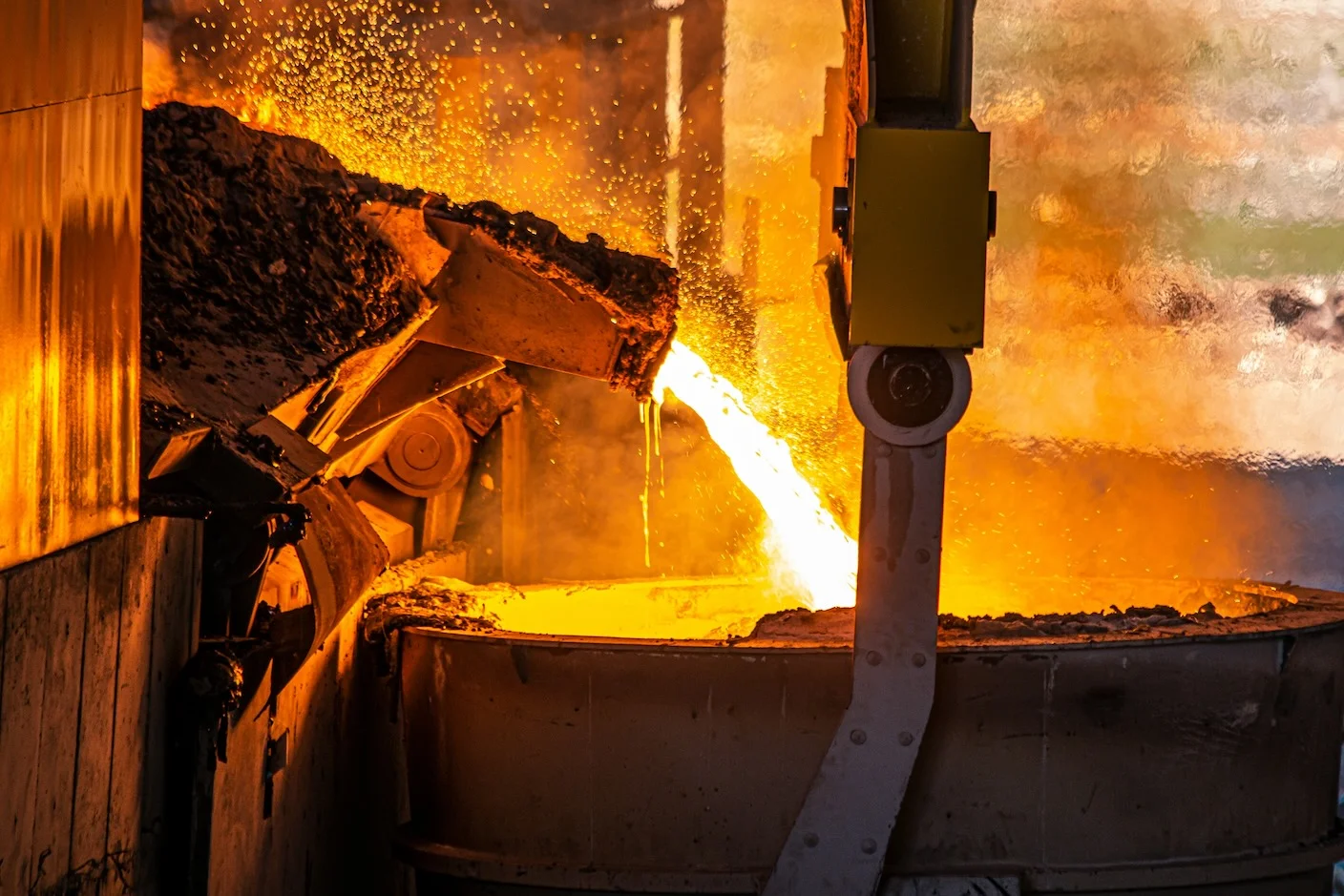
For Boston Metal, it’s a step towards green steel plants that can make millions of tons of steel.
Steelmaking is one of the hardest industries to decarbonize due to its reliance on high temperatures and coal-based fuels to drive crucial reactions. But a green steel company has made a major breakthrough after its new plant produced more than a ton of the metal.
Rapid progress decarbonizing the energy and transport sectors is leading to a growing focus on areas of the economy where it will be harder to ditch fossil fuels. One of these is steelmaking, which by some estimates produces as much as 8 percent of all carbon emissions.
US startup Boston Metal hopes to change this by commercializing zero-emission steelmaking technology developed at the Massachusetts Institute of Technology. This week, the company completed the first run of its largest reactor yet, which validates key technologies required to start producing steel at industrial scales.
“With this milestone, we are taking a major step forward in making green steel a reality, and we’re doing it right here in the US, demonstrating the critical innovation that can enhance domestic manufacturing,” Tadeu Carneiro, CEO of Boston Metal, said in a press release.
Traditional steelmaking involves burning a coal-based fuel called coke, both to generate the high temperatures required and to remove oxygen from iron ore to create iron. But this generates huge amounts of CO2, which is why steelmaking is so bad for the environment.
Boston Metal’s approach instead uses electrolysis to convert iron ore into molten iron without directly producing any emissions. As a result, if the electricity used to drive the process comes from renewable sources, the resulting metal is almost entirely emission-free.
The company’s process, known as molten oxide electrolysis, involves mixing iron ore with an electrolyte inside a large reactor, heating it to 2,900 degrees Fahrenheit, and then passing a current through it.
The oxygen in the ore separates and bubbles up through the electrolyte, while a layer of molten iron collects at the bottom of the reactor. This reservoir of liquid metal is then periodically tapped, though the process itself is continuous.
One of the biggest challenges for the approach is creating an anode—the positive terminal used to introduce electricity to the reactor—that doesn’t degrade too rapidly. A short shelf life for this component would mean regular stoppages for maintenance or replacement, which would significantly impact the approach’s commercial viability.
Adam Rauwerdink, Boston Metal’s senior vice president of business development, told MIT Technology Review that the company has successfully made their anodes hardier. But the new bus-sized reactor is the first to feature multiple anodes, which will be key to scaling the approach.
The current plant can produce a ton or two of metal in about a month. However, the company hopes to build a plant that can produce the same amount in a day by the end of 2027. The design is modular, and the plan is to eventually string many reactors together in facilities that can output millions of tons of steel.
Boston Metal is not the only company attempting to clean up steelmaking.
Swedish company Stegra has raised billions of dollars to build the world’s first large-scale green steel plant in Northern Sweden. The plant will use green hydrogen to cut emissions by up to 95 percent. US startup Electra is also raising $257 million to develop a low-temperature electrochemical process for producing green iron.
Scaling any of these approaches to the point where they make a dent in an industry as massive as steelmaking will be a huge challenge. But these developments suggest the technical barriers are rapidly falling.
The post Green Steel Startup’s Largest Reactor Yet Produces a Ton of Molten Metal With Electricity appeared first on SingularityHub.
* This article was originally published at Singularity Hub
0 Comments